在液流电池领域,双极板作为电堆的核心零部件,扮演着至关重要的角色。它不仅是相邻单电池之间的导电桥梁,串联多个单电池形成电堆以提升整体电压,还负责收集并传导电极反应产生的电流,确保电能的高效输出。因此,双极板的性能直接决定了液流电池的能量效率、功率密度和寿命。
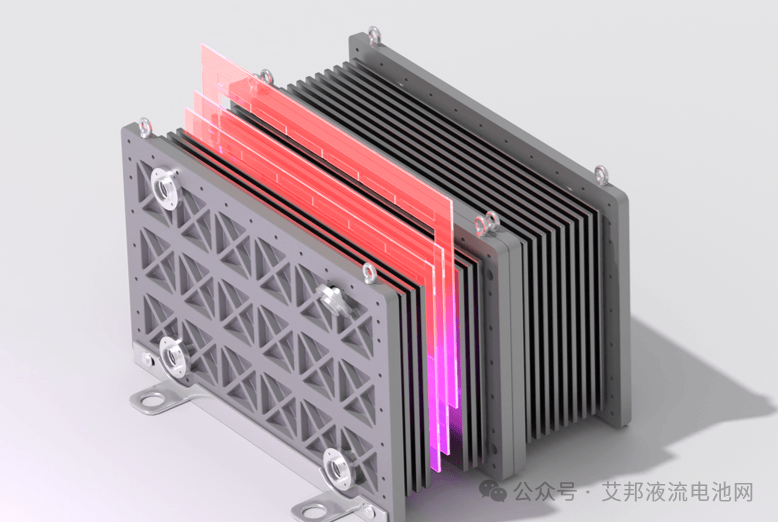
杜科新材通过系统性技术创新与全产业链布局,在液流电池石墨双极板领域实现了从材料研发到规模化生产的突破,成为行业技术革新的标杆。以下从技术路径、工艺创新、产能布局及行业影响等角度补充优化分析:
一、技术革新路径:全流程自主化与性能突破
1. 原材料优化与硫插层技术
杜科新材精选高纯度天然石墨粉,通过磁选提纯工艺,从源头保障双极板材料的高纯度,并进一步采用硫插层高温膨化技术制备高含碳量石墨蠕虫,将硫含量降至500PPM以下,铁含量严格控制在50PPM以内,显著提升材料的导电性(电导率达600S/cm),保障双极板性能的稳定性。
采用自合成树脂胶与石墨粉混合,提升极板抗弯强度,进一步提高了电池的能量密度和循环寿命。
2. 板胶一体化战略和微孔封堵技术
杜科新材首创“板胶合一”生产模式,将双极板与粘接密封胶紧密结合。推出DB750L系列胶水密封粘接方案,不仅减少了胶水使用量和粘接过程中的浪费,还提高了组件的密封性和稳定性。
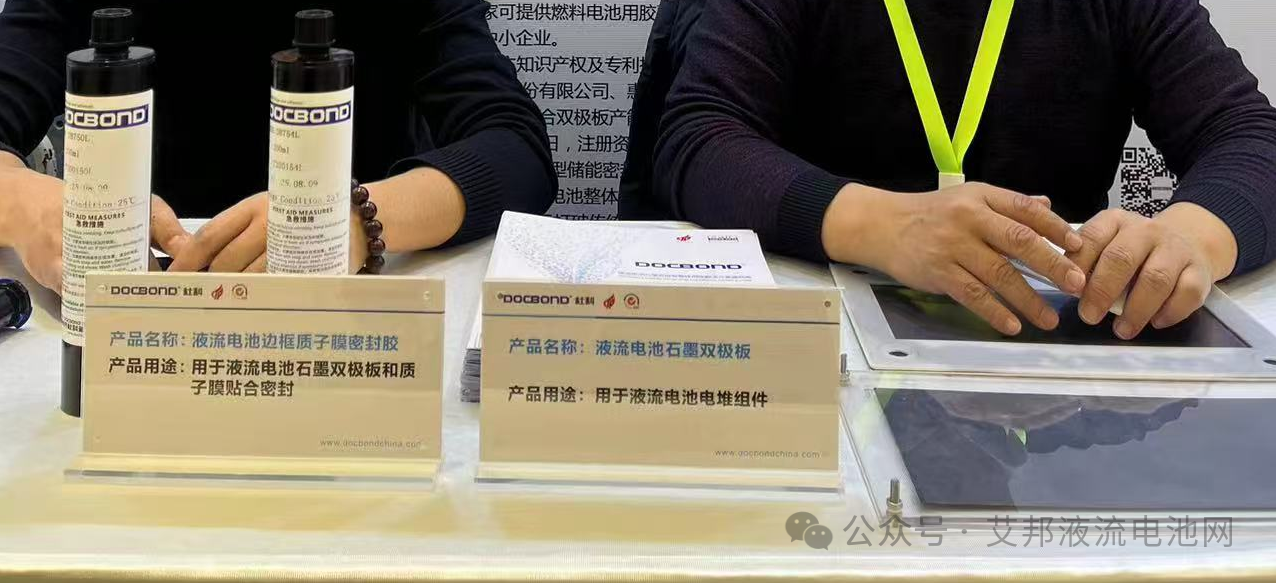
二、工艺创新:高精度制造与成本控制
1.冷压成型与辊压浸渍工艺
杜科突破传统热压工艺限制,采用冷压成型技术简化流程,结合辊压成型与浸渍工艺,实现双极板的高密度、均匀结构。此工艺使产品厚度误差控制在±0.05mm,表面粗糙度低于1.6μm,满足液流电池对极板平整度的严苛要求。
与市场上通用的热压成型工艺相比,杜科采用的冷压成型工艺,成型速度更快,大概30秒钟就可以成型一块极板,在如果是一模两切,可以做到30秒成型两块极板。
三、产能布局与产业链协同
1. 规模化生产与产能规划
江西杜科已建成年产100万平方米液流电池双极板生产线,配套自动化产线实现单日3000片产能,良品率达98%。同时规划扩建年产50万平方米氢燃料电池碳纸/碳毡产线,延伸至液流电池上游材料领域。
2. 战略合作生态构建
与中海储能、液流储能等头部企业签订供货协议,并联合陕西科技大学院士团队成立核心材料研发中心,推动产学研深度融合。此外,通过参与国家示范项目装堆测试,产品获头部客户认证,加速商业化落地。
四、行业影响与市场价值
1.打破进口依赖
杜科双极板实现关键性能指标超越进口产品(如导电性提升15%,成本降低40%),推动国产替代进程。其技术被纳入8个国家示范项目,支撑百兆瓦级液流电池项目建设。
2.助推储能降本
通过规模化生产与工艺优化,双极板单价降至120元/平方米以下,助力液流电池系统成本突破1.5元/Wh门槛,加速长时储能商业化。
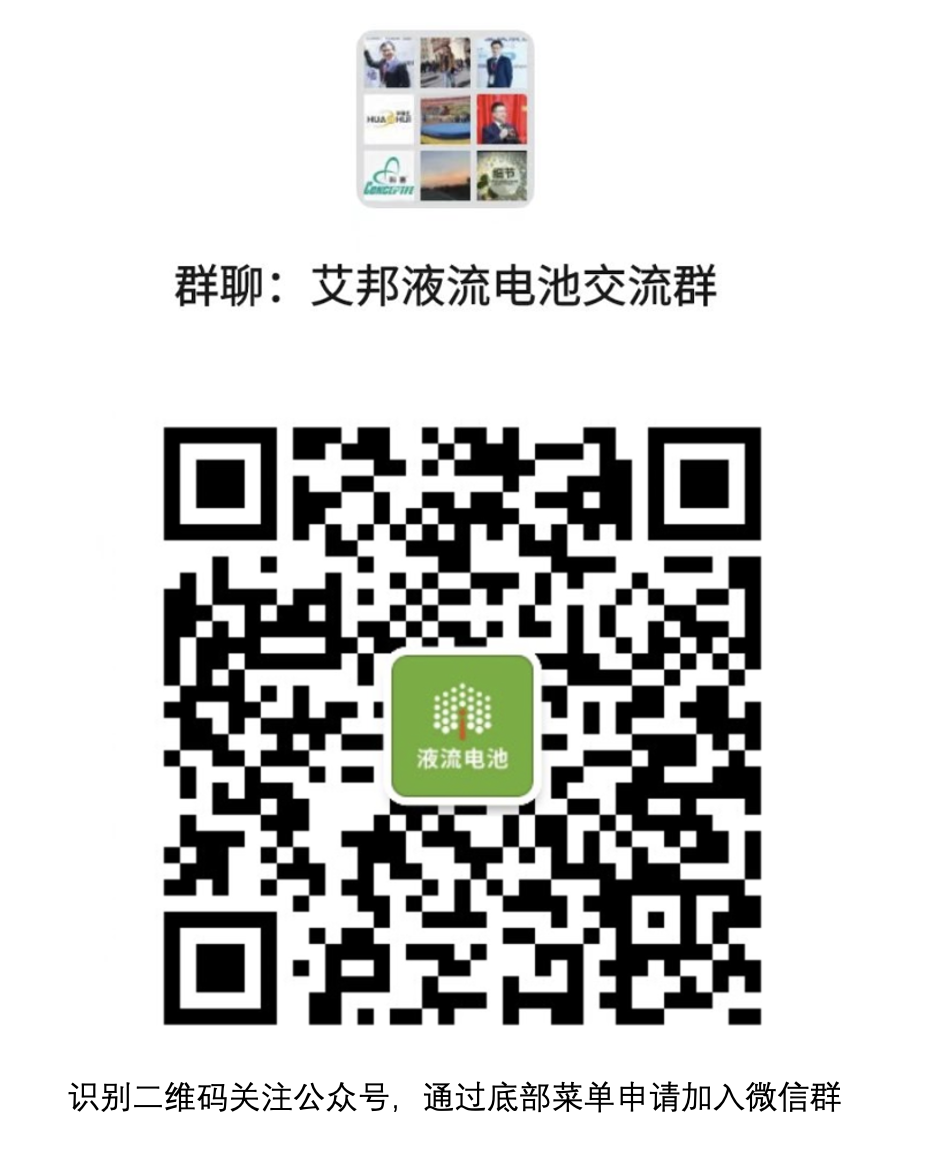