液流储能电堆是按照压滤机的方式进行组装,双极板在电池组中实现单体电池间的连接,隔离相邻单体电池间的电解质溶液,同时收集双极板两侧电极反应所产生的电流。此外,电堆中的电极要求一定的形变量,双极板对其提供刚性支撑。
液流电池工作原理、电堆结构及关键零部件
(1) 导电性优良,连接单体电池的欧姆电阻小且便于集流。
(2) 良好的机械强度和韧性,既能很好地支撑电极材料,又不至于在密封电池的压紧力作用下发生脆裂或破碎。
(3) 良好的致密性,保持不发生渗液和漏液,避免相邻单体电池之间的电解质溶液出现互混。
(4) 良好的耐酸性和耐腐蚀性。在全钒液流电池体系中这一点尤为重要,该体系采用强酸作为支持电解质,正极的五价钒(VO)具有很强的氧化性。另外,处于较高的电极电位下就形成了苛刻的强酸、强化学氧化和电化学氧化环境。
全钒液流电池通常采用孔隙率比较大的碳毡或石墨毡作为电极,电解质溶液在电极内部流动,无须像质子交换膜燃料电池那样在双极板表面刻制流场,但要求双极板表面平整,与电极的接触电阻要小。对于全钒液流电池双极板材料,一般使用石墨板以及碳塑复合材料板。
非贵金属材料在全钒体系的强酸强氧化性环境中易被腐蚀或形成导电性差的钝化膜,铂、金、钛等金属虽然耐腐蚀性较好,但价格高昂,不适合规模化应用。人们通过电镀、化学沉积等方法对不锈钢材进行表面处理,以增强其耐腐蚀性,提高其作为双极板的使用寿命,但效果甚微,仍然无法在全钒液流储能电池的运行环境中长期稳定工作。因此,金属材料并不适合用于酸性电解质溶液液流电池的双极板材料,目前鲜有该类材料的研究。
石墨材料在全钒液流电池运行条件下具有优良的导电性、耐酸腐蚀性和化学及电化学稳定性。无孔硬石墨板材料致密,能有效阻止电解质溶液的渗透。这些特性使硬石墨板适合用于全钒液流电池双极板板材。
但硬石墨板制备工艺相当复杂,能耗大。一般采用石粉与可石墨化的树脂或沥青混合,经复杂的制造工艺,在石墨化炉中严格按一定的升温程序,升温至2500℃~2700℃,制备出无孔或低孔隙率的仅含纳米级孔的石墨块,再经切割和研,制备出所需厚度的石墨板,耗时多,成本高。而且无孔石墨双极板材料的脆性强、韧性差,用于大功率电堆时,在压紧密封过程中容易破碎,限制了石墨板在液流电池中的应用。
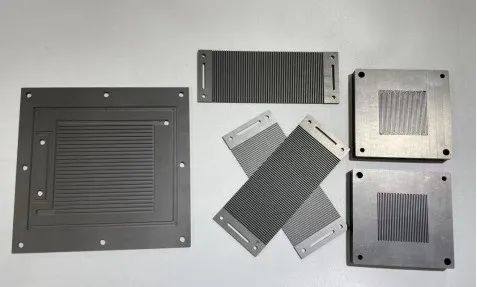
目前,大功率液流电池电堆中使用的是碳塑复合双极板。碳塑复合双极板材料一般采用导电碳粉(如石墨粉、炭黑、碳纤维等)与热塑性树脂(如聚乙烯、聚氣乙烯、聚丙烯等)及阻滞剂、脱模剂等均匀混合,通过注塑或模压的方法制备碳塑复合双极板。碳材料作为导电填料提供导电性,树脂作为黏结剂提供机械强度并填充碳材料之间的孔隙。
复合双极板由于用于成型黏结剂的树脂未经炭化,所以极板的本体电阻远高于石墨双极板,而且碳塑复合双极板与电极的接触电阻也高于石墨双极板与电极的接触电阻。
双极板制造流程有以下几个重要步骤:模压-浸渍-固化-烘干整平-点胶-粘接-固化-检测(各企业工艺有所调整)。
复合双极板的加工工艺:
目前,注塑成型工艺和模压成型工艺是复合材料双极板加工的两种常用方法。由注塑成型工艺发展出来的传递模塑工艺和反应注塑工艺也被用来加工复合材料双极板。注塑成型工艺是较模压成型工艺更加常用的方法,但是由于受到物料流动性的影响,不能制备聚合物含量较低的复合材料双极板,由此而导致双极板导电性较差。
挤出成型工艺是通过将复合材料在具有螺杆的旋转筒体中混合软化,然后挤出到模具中,经过一段时间的冷却固化将模具打开并将复合双极板顶出,通常是半自动化甚至自动化的工艺过程。
模压成型工艺是将混合好的复合材料置于模具中,在热压机中加热并施加一定压力,然后保温保压一定时间,最后冷却固化、卸压开模。
目前在液流电池双极板领域,以石墨双极板和碳塑双极板为主。为了满足定制化需求和控制成本,不少液流电池选择自己制造双极板材料,如恒安储能、新新钒钛、宿迁时代、开封时代、美淼储能等。
此外不少氢能领域极板工艺供应也开始布局液流电池极板。
南海碳材(柔性石墨双极板/流道双极板)、华熔科技(复合板碳塑/柔性/等静压石墨双极板)、杜科新材(石墨板+粘结胶+PP板一体样件)、纳科新材、环华氢能、博远(山东)新能源(石墨双极板、金属双极板)、弘枫实业(石墨质流道双极板)、山东鼎誉新能(柔性石墨双极板)、金博股份、骊能新能源、旭能瀚源(碳塑双极板)、嘉兴纳科新材、青岛一苇新材(碳塑复合双极板)、保定市正念复合材料(聚丙烯/PP基材型耐腐蚀塑料双极板)、湖南耕驰新能源(高性能碳基模压复合双极板)、嘉裕碳素(金属双极板 &石墨双极板)、辽宁科京(挤出石墨双极板)等。
来源艾邦液流电池网综合整理,仅供行业参考,如需转载,请注明出处。