全钒氧化还原液流电池具有设计灵活、放电深度大、响应速度快、循环寿命长等优点,是一种有潜力的可再生能源储能系统。为了最大限度地减少由于分流电流造成的能量损失,在传统的设计中,流场是在两个电绝缘的框架上加工的,中间是石墨板。
传统的全钒液流电池双极板(BP)由许多部件组成,因此,装配过程非常耗时。在本研究中,设计和制造了一个整体成型的BP,以最小化制造成本。首先,通过仿真分析了模具设计和注射参数对机架成形性的影响。其次,提出了一种新的整体成型石墨板设计方案,最后对两种整体成型石墨板进行了制作和比较。结果表明,闸门位置对疏气阀有显著影响,最大体积收缩发生在BP的拐角处。体积收缩可以减少使用一个大石墨板嵌入框架内。
关键词:全钒氧化还原液流电池;双极板(BP);注射成型;能量储存
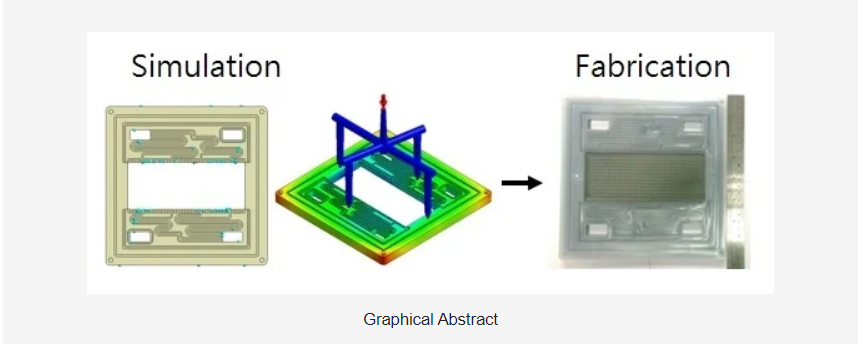
1. 介绍
太阳能和风能不是稳定的能源,因为它们的发电取决于天气。为了提高电力系统的稳定性和可靠性,需要建立储能系统来节约多余的电能,平衡电力供需。在储能系统中,全钒氧化还原液流电池(vrb)因其设计灵活、响应时间快、循环寿命长、能效高、维护成本低等特点而备受关注。
在VRB系统中,正负极电解质通过泵从VRB堆再循环到电解液储罐;因此,能量容量和功率可以分开设计。能量容量取决于电解质的数量,而功率取决于VRB堆叠的大小。VRB体系的化学能存储在钒离子的不同价态(V5+、V4+、V3+和V2+)。在VRB中发生的反应如下。积极的一面:
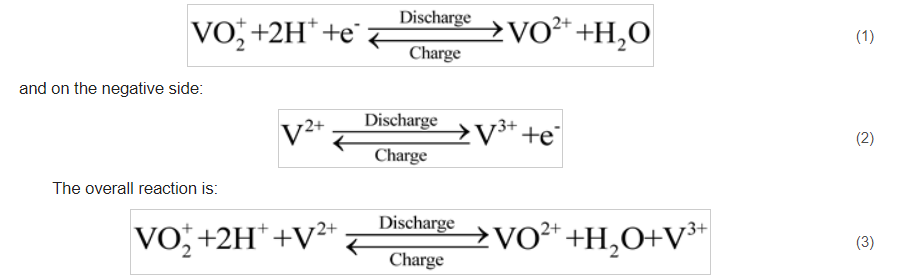
迄今为止,VRB系统的商业化仍面临一些挑战,包括其低能量密度和钒品种和其他关键部件的高成本。VRB堆叠通常由双极板(bp)、多孔电极和离子交换膜组成。VRB中双极板的主要功能是支持堆叠结构,分离正负极电解质,并在电池间连接电路径。
许多研究人员都专注于开发双极板(bp)。为了降低传统石墨板的制造成本,研究了碳-聚合物复合材料。由于聚合物结构不导电,因此添加导电填料对于达到所需的导电性至关重要。石墨纤维、碳纤维、碳黑和碳纳米管已被用作燃料电池中bp的导电填料。研究的重点是填料的分散和分布、填料与聚合物基体的相互作用以及填料的电学和力学性能。
由于全钒液流电池(VRB)中存在酸性电解质,燃料电池应用中的bp不能直接用于vrb。由于BP需要在酸性环境中工作,因此它们的化学稳定性对BP材料的选择至关重要.
-
Lee等人开发了不同聚合物的复合bp,并研究了石墨涂层碳复合bp[12]的耐久性。
-
Caglar等人使用钛酸盐基偶联剂和碳纳米管架桥石墨颗粒。实验结果表明,填料的分散性得到改善,bp的通面电导率和面内电导率之差减小。
-
Lee等人通过压缩成型开发了不同炭黑含量的碳复合bp,并表明炭黑含量为15 wt%的bp在vrb工作环境中具有良好的导电性和提高的电化学稳定性。
-
Park等人以双酚A二甘油酯醚芳香族环氧树脂为聚合物基体,二氨基二苯砜为固化剂,石墨薄片和碳颗粒为填料制备bp,并确定了VRB堆中稳定复合bp的最佳组成。
全钒液流电池(VRB)的双极板(BP)由两部分组成:电绝缘框架和导电石墨板。
由于VRB的电解质具有导电性,因此在电池之间会产生分流电流,从而导致性能下降。可以使用电绝缘框架将分流电流减小到有源区域的外围。一种常见的传统BP设计如图1a所示。如图所示,石墨与框架的接触面需要垫片,以防止电解液泄漏。显然,VRB堆栈中的泄漏需要解决。
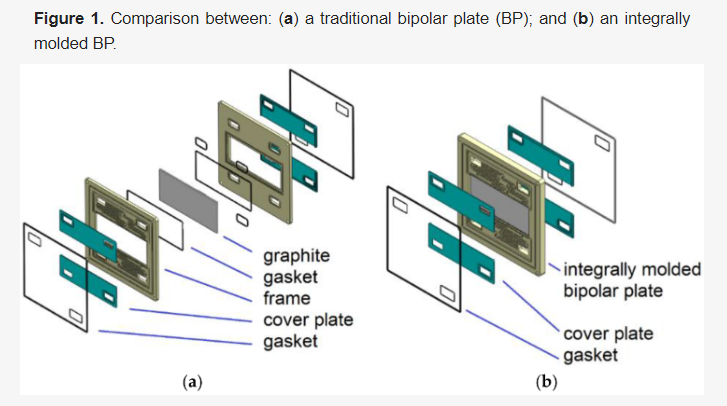
据我们所知,迄今为止,vrb中bp的泄漏问题尚未得到广泛的研究。一些研究集中在改善石墨板和框架之间的结合。
-
Soohyun等人开发了一种智能固化循环,以降低共固化e -玻璃/碳/环氧复合材料BP的热残余应力。采用智能固化循环,BP挠度降低32%。
-
住友电气工业公司设计了一个由50%以上的氯乙烯和复合石墨板组成的框架。采用改进的胶粘剂将骨架与石墨板粘结在一起,增强了密封性。他们还为垫圈设计了内部和外部密封槽,以防止电解液泄漏。
-
这些研究侧重于防止石墨板和框架之间的泄漏,从而增加制造成本和组装时间。为了减少组件的数量,BP可以通过注射成型制造。此外,石墨板和框架之间的泄漏风险可以减少。
-
dos Santos等人提出了一种石墨板模塑框架;然而,在他们的报告中没有研究模具设计和注射参数。
在本研究中,设计和制造了一个整体成型的BP通过注射成型。图1b显示了整体成型的BP。首先,通过仿真研究了浇口位置和注射参数对框架成形性能的影响。讨论了石墨板设计对成形性能的影响。
2. 模具设计与分析
本研究旨在开发一个整体成型的BP,其活动面积为100平方厘米。研究了模具设计和注射参数对BP成形性能的影响。将尺寸为17 cm × 8 cm × 5 cm的石墨板在石墨电极两侧的中心加工成16 cm × 6.5 cm × 1 cm。在有源区周围加工两个通道,防止电解液泄漏,如图2a所示。在注射成型框架上设计了一种改善电解质分布的流场模式,如图2b所示。
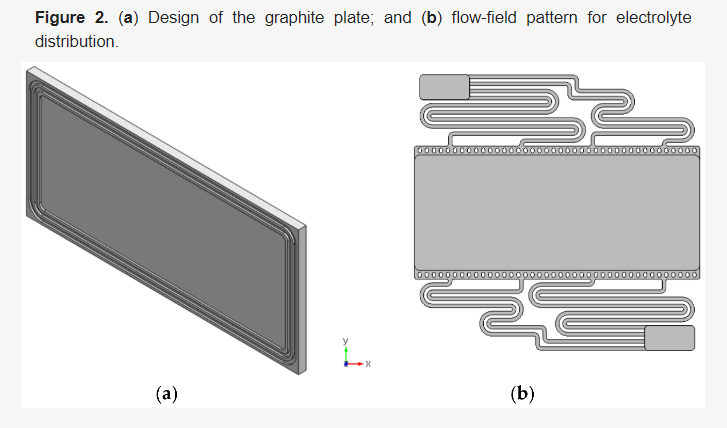
2.1. 控制方程
注射框架的成形性取决于熔化的聚合物在模具中的流动行为。在注射成型过程中,假定熔融的聚合物表现为广义牛顿流体。模腔内的非等温聚合物树脂可以用以下方程来描述:
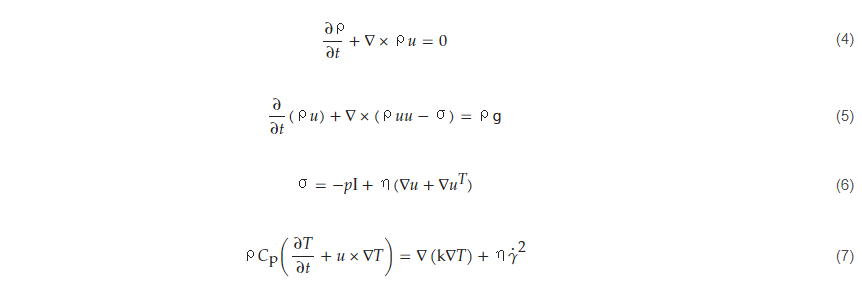
其中u为速度矢量,T为温度,p为压力,σ为总应力张量,ρ为流体密度,η为粘度,k为导热系数,Cp为比热,<s:1>˙是剪切速率。在本研究中,采用具有Arrhenius温度依赖性的修正cross模型来描述熔融聚合物的粘度:
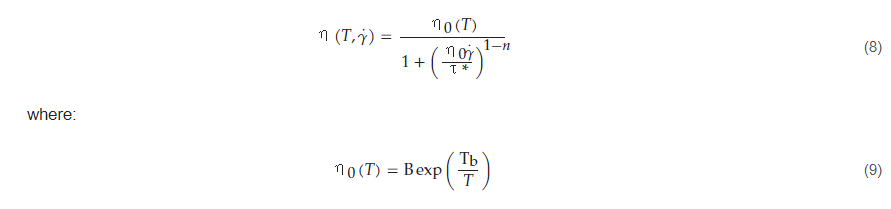
其中η0为零剪切粘度,τ为描述粘度曲线的零剪切速率区与幂律区之间过渡区域的参数,n为幂律指数,B为指数拟合常数,T* B为温度拟合常数。
由于在Moldex3D中模拟的是注塑材料的行为,因此只需要构建完整的框架模型,如图3所示。采用SolidWorks建立框架模型,导入到Moldex3D中进行注塑建模仿真。在运行仿真之前,需要在Moldex3D中设置浇口位置和操作参数,如聚合物温度、成型温度、注射压力、保持压力和环境温度。框架材料选用聚丙烯(PP)。模拟中使用的PP的粘度、比热、比容等物理性能是温度的函数,由Moldex3D提供,如图4所示。
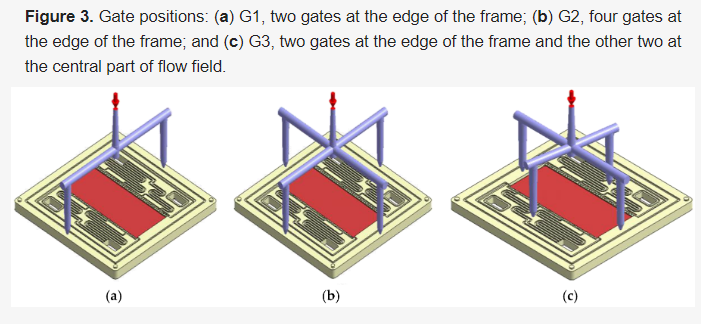
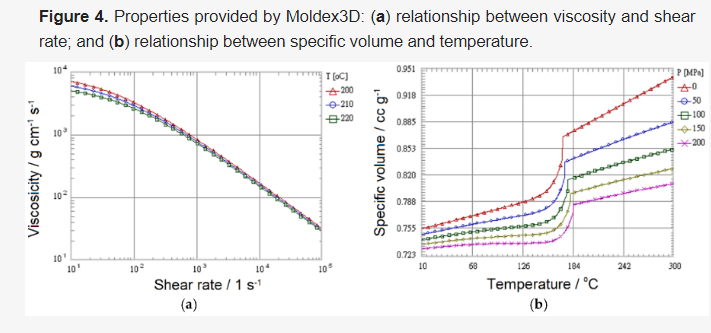
图4。Moldex3D提供的特性:
(a)粘度与剪切速率的关系;(b)比容与温度的关系。
2.2. 注射口位置
图3显示了三种闸门位置设计。大门的位置在框架的一个不起眼的地方;因此,在框架上只有少数合适的区域。在G1中,在边框边缘放置两个栅极,如图3a所示。在G2中,在框架边缘设计了4个栅极,如图3b所示。在G3中,两个栅极位于框架边缘,另外两个位于流场中心,如图3c所示。
2.3. 注射参数
此外,该软件还建议了每种常用聚合物的注射参数。例如,PP的建议参数值如表1中的情形P1所示。研究了注射压力和聚合物温度对BP成形性的影响。P2、P3和P4的注入压力分别为100、180和220 MPa。P5和P6的熔融聚合物温度分别为200℃和220℃。在所有模拟情况下,成型温度为60°C,环境温度为25°C。
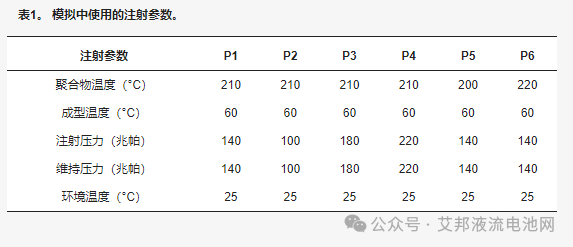
3. 结果与讨论
注射口的位置和注射参数对成形性的影响将在接下来的章节中讨论。
3.1. 浇口位置对成形性的影响
成型产品的可成形性可以通过一些空气陷阱和体积收缩来评估。疏气阀通常位于融化的聚合物最后填充的地方。被截留的空气会在模塑件内产生气泡或空洞,或表面缺陷。体积收缩可能造成尺寸误差,导致电解液泄漏。在考虑闸门位置时,需要尽量减少疏气阀的数量和体积收缩。
对于VRB的BP,只有几个位置适合放置栅极。在充填停止前,注入物料应同时完全填充所有空间,同时保持压力分布均匀。闸门位置对疏气阀的影响如图5所示。通过Moldex3D可以量化疏气阀的数量。从图中可以看出,G3的空气疏水阀个数为112个,而G1和G2的分别为178个和175个,这是由于流场中心的闸门有助于将注入物从中心区域分散。
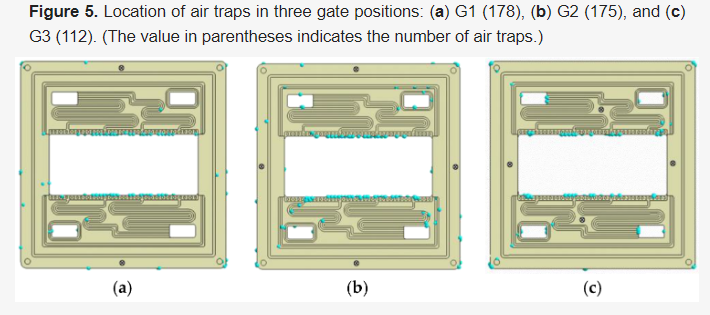
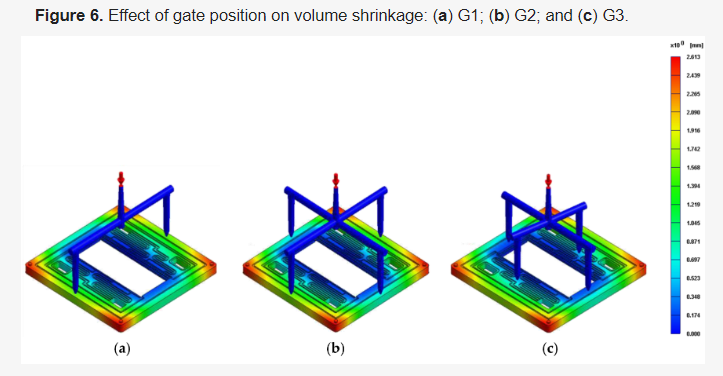
3.2. 注射参数对成形性的影响
图7显示了P1、P2、P3、P4、P5和P6的模拟结果中的空气阱。通过对比图7a-d可以研究注射压力对成形性的影响。可以看出,当喷射压力在100 ~ 220 MPa范围内变化时,疏气阀的位置与P1几乎相同,两种情况下的疏气阀个数均为112个。
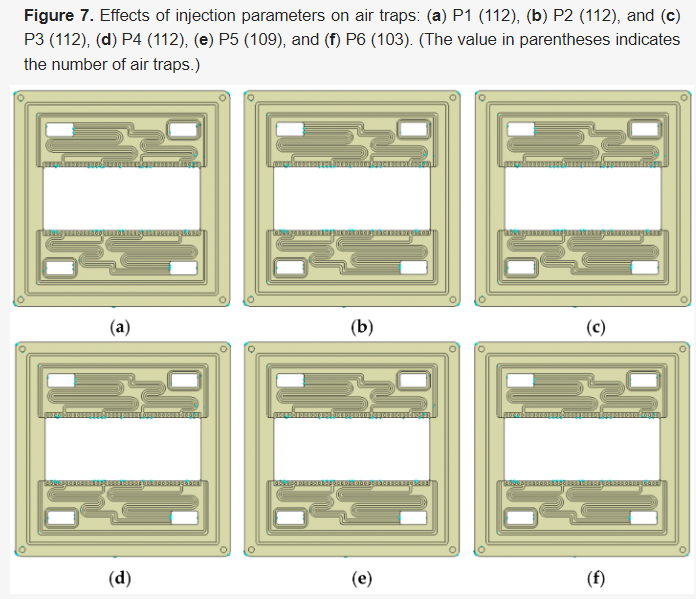
图7. 注射参数对气室的影响: (a )P1(112), (b)P2(112), 和(c)P3(112), (d)P4 (112),(e)P5(109), 和(f )P6(103)。(括号中的值表示空气陷阱的数量。)
对比图7a、e、f可知,当聚合物温度从200℃升高到220℃时,气疏水阀的数量和位置变化不大,但趋势不明显,P5为109个,P6为103个。
此外,在所有情况下(P1到P6),体积收缩在2.6到2.8 mm之间,如图8所示。最大收缩发生在模塑框架的四个角。从图7和图8可以看出,选择不同的注入参数值并不会显著降低体积收缩率。
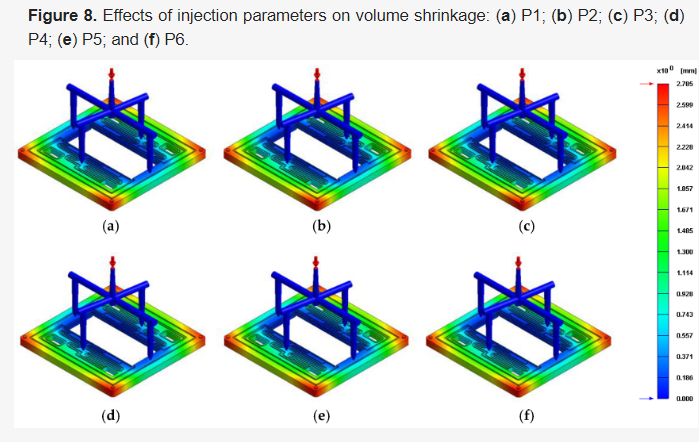
图8. 注射参数对体积收缩的影响:( a )P1;( b )P2;( c ) P3;( d ) P4;( e ) P5;以及 ( f ) P6.
根据前几节的讨论,可以通过选择适当的闸门位置来减少空气疏水阀;然而,体积收缩不能通过改变浇口位置或注射参数来显著减少。由于在框架的角落区域内没有石墨板来支撑聚合物材料,因此最大的收缩发生在四个角落。
3.3. 双极板的改进设计
体积收缩发生在石墨板区域外相对较厚的注入材料处。因此,为了尽量减少拐角周围的收缩,石墨板被重新设计为具有更大的面积,从而可以减少覆盖石墨板的注射材料的厚度。图9显示了两种新的石墨板设计,一种是在外围没有肋,如图9a所示,另一种是有肋,以提高抗弯强度,如图9b所示。
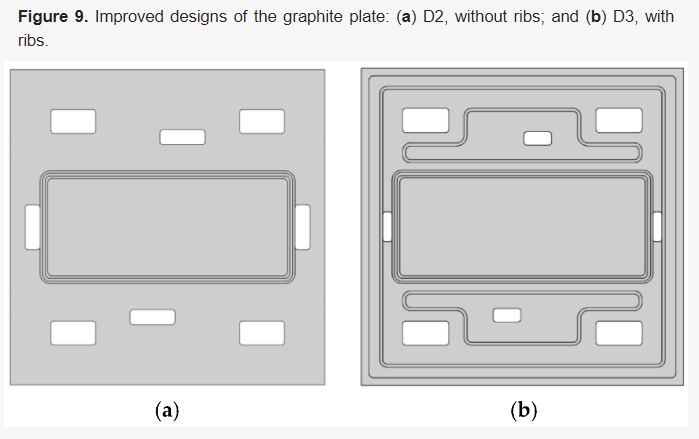
图9. 改进的石墨板设计: ( a ) D2,无肋;和 ( b ) D3,有肋。
D2和D3注入bp的模拟气阱如图10所示。D2和D3的疏气阀数量分别为134个和158个,比原设计(G3)多。由于所有三种设计中的浇口位置都是相同的,因此预计二次流场是填充注入材料的最后区域。因此,石墨设计不影响空气疏水阀;影响陷阱的是闸门的位置。
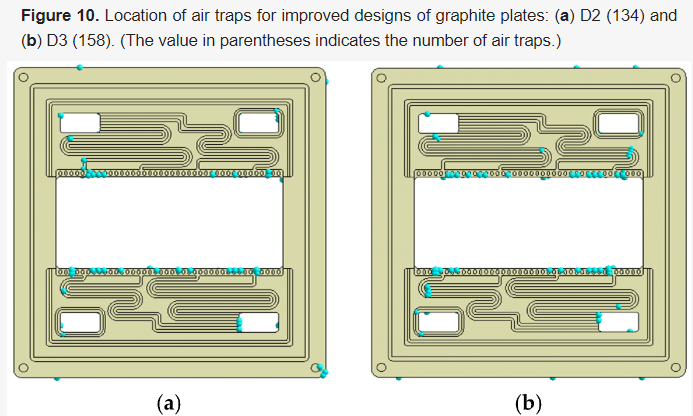
D2和D3的模拟体积收缩如图11所示。D2和D3的最大收缩量分别约为0.43和0.38 mm。与原设计(G3)相比,较大的石墨板显著降低了注射材料的收缩率。模拟结果显示,D3的体积收缩率小于D2。由于在D3中石墨板的外围存在罗纹,因此在角落处注入的聚合物材料的厚度和体积收缩率都降低了。
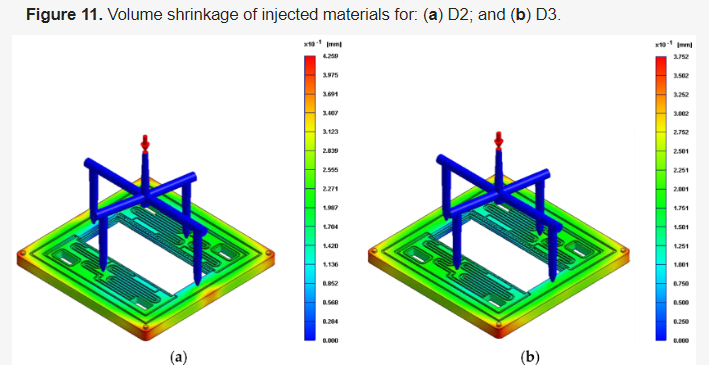
图12显示了不同嵌入石墨板的整体成型bp。在图12a中,具有相对较小石墨板的BP在四角处显示出显着的体积收缩。将石墨板更换为较大的石墨板后,边角处的体积收缩明显减小,如图12b所示。虽然通过适当设计嵌入式石墨板可以最大限度地减少体积收缩,但成型bp的平整度对堆叠组件也至关重要。因此,在未来,将研究成型bp的平整度。
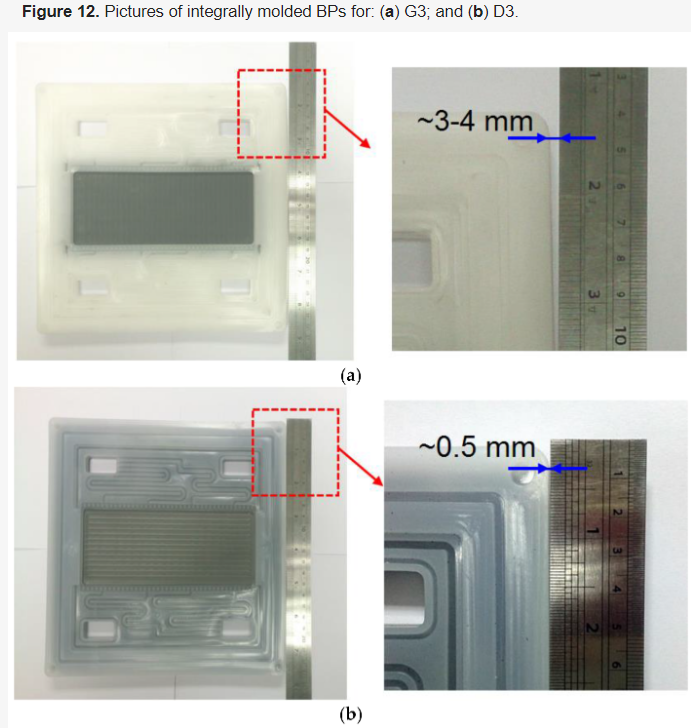
4. 结论
bp是vrb的关键组成部分。为了减少部件数量和简化装配过程,设计和制造了整体成型bp。利用商业软件Modex3D进行了数值模拟,研究了浇口位置和注射参数对BP成形性能的影响。所得结论如下:
-
闸板位置对疏气阀有显著影响。位于流场中心部分的闸门减少了空气疏水阀的数量。
-
由于注入的材料相对较厚,BP的角部会出现最大体积收缩。
-
使用角部最大收缩约为0.4毫米的大型石墨板可以减少体积收缩。
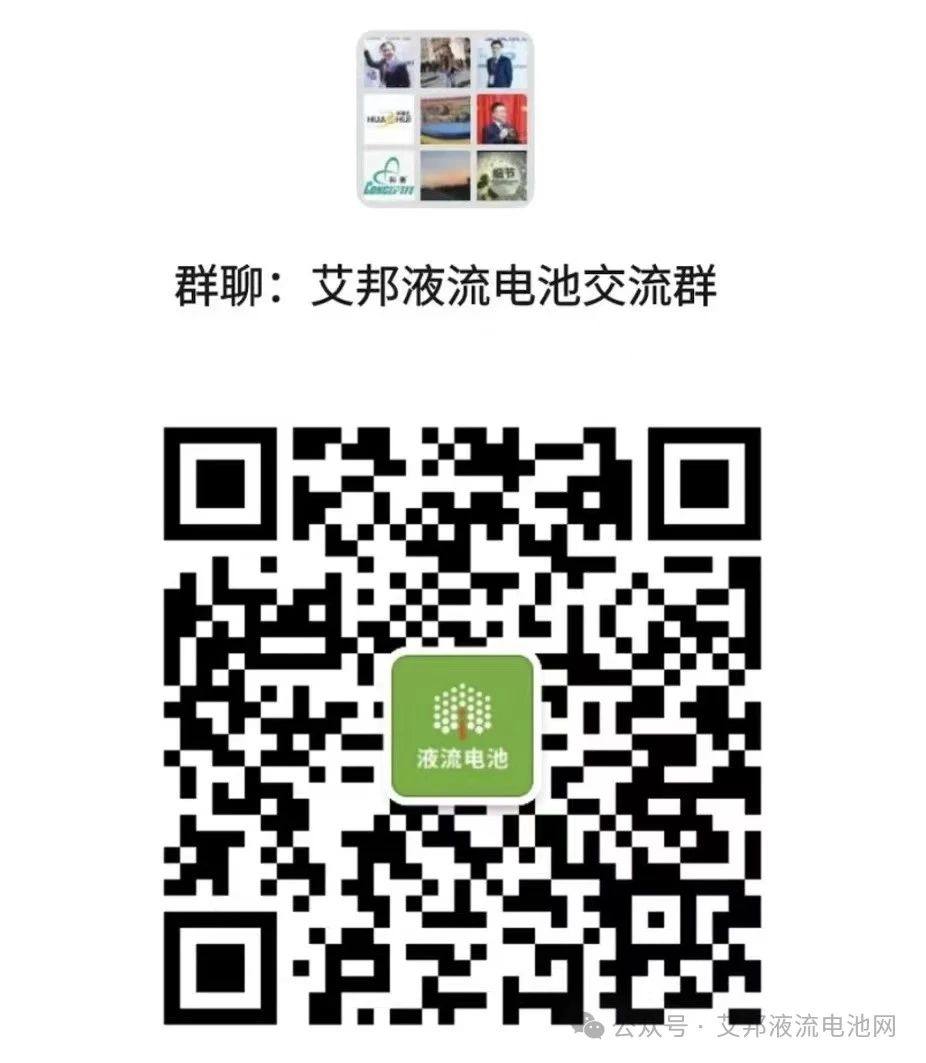
第二届全国液流电池大会
会议议题(包括但不限于)
序号 |
拟定议题 |
1 |
液流电池储能技术的发展现状与市场前景 |
2 |
液流电池产业链搭建的核心环节、挑战与降本路径 |
3 |
液流电池在新型电力系统中的多重价值与效益转化机制 |
4 |
液流电池系统集成技术方案与常见问题分析 |
5 |
液流电池储能管理系统健康管理技术革新 |
6 |
液流电池BMS的设计挑战与创新 |
7 |
液流电池电堆结构设计与性能提升 |
8 |
全钒液流电池关键材料的研究进展与产业化应用 |
9 |
铁铬/铁系液流电池长时储能技术瓶颈与商业化突破 |
10 |
锌溴/锌铁液流电池技术研究进展与产业化实践探索 |
11 |
水系有机液流的关键技术和材料研究 |
12 |
液流电池电堆组装工艺与产线设备关键技术 |
13 |
液流电池批量化生产工艺、设备及其生产线介绍 |
14 |
钒电解液供应链发展现状与未来趋势 |
15 |
液流电池电极结构优化与规模化生产挑战 |
16 |
液流电池离子膜低成本制备策略与应用场景 |
17 |
液流电池高性能双极板复合结构设计与制备工艺 |
18 |
液流电池的密封技术与工艺创新 |
Mickey周丹: 18320865613(同微信)
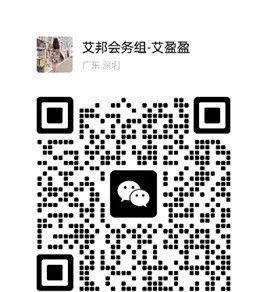
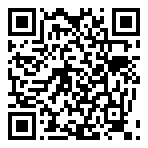
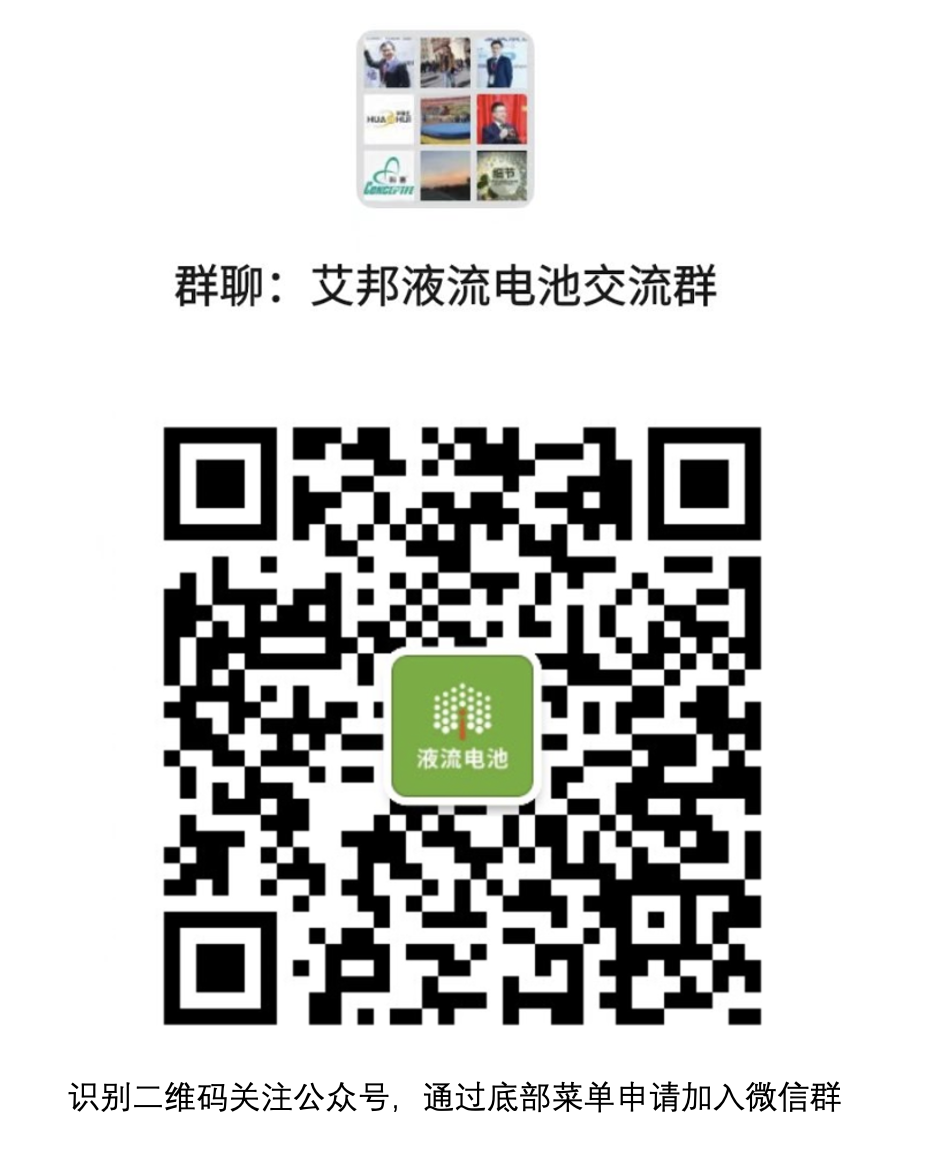